Stop Herding Cats – Optimise Them
- SIG ML
- May 20
- 4 min read
How intelligent optimisation and control strategies help teams move from reactive wrangling to proactive performance

If you’ve ever felt like your operations are one step away from chaos, you’re not alone.
Every day, engineering and operations teams try to wrangle dozens of unpredictable, interdependent variables — from equipment behaviour and environmental shifts to conflicting constraints across systems.
It’s a bit like herding cats.
The tools might be there — dashboards, data feeds, models — but turning all that into timely, effective action? That’s where things can fall apart.
While most teams have some process for optimisation and control, it’s often slow, siloed, or reactive. They might be unaware that better optimisation/control is even achievable, and even if they are there’s an understandable need for a compelling business case before even considering buy-in.
The Quiet Cost of Operational Lag
Modern operations generate more data than ever. Yet despite that, decision-making is often slow, reactive, and based on limited insights. Teams are still running disconnected models, or relying on gut feel to respond to events that already happened.
This approach might keep things running, but it’s holding performance back. You may not see it explicitly — but you’ll feel it in downtime, overcorrections, and delayed interventions, all of which translate into lost output, unnecessary costs, and growing frustration.
Traditional Tools Are Reaching Their Limits
Engineering teams have long relied on a familiar mix of modelling software, manual workflows, and rule-based control systems. But those tools weren’t designed for today’s operating environment.
Traditional modelling is static. Models struggle to adapt quickly. They’re hard to scale. And most importantly, they don’t plug into the daily rhythm of real-world operations. Even when the data is there, the path to action is slow and uncertain.
Why This Needs to Change Now
Let’s be honest: most teams aren’t drowning in a lack of information. They’re drowning in decisions.
The real bottleneck isn’t data, it’s how quickly it’s made available and what happens between detection and action.
Here’s the commercial reality:
Downtime still dominates costs, especially when issues are spotted too late.
Efficiency gains are getting harder to find.
Talent is stretched thin, with senior engineers spending time chasing symptoms and making trade-offs, rather than solving root problems.
What’s missing isn’t effort or expertise. It’s structure — the kind that lets teams make fast, confident decisions based on real-time conditions, not lagging reports.
Advanced optimisation and intelligent control bring that structure. They embed predictability into decision-making, enabling your systems to self-adjust, flag emerging issues, and recommend the next best move in real time.
That means faster interventions, better throughput, and less fires to put out. All without having to rip and replace your existing systems.
What It Looks Like in Practice
So what does it look like to embed advanced optimisation and control tools into day-to-day operations?
It’s not about adding more dashboards, it’s about giving your team the ability to:
Detect and interpret deviations from expected performance - early, not after the fact.
Run simulations on-the-fly to evaluate different operational strategies and trade-offs.
Automatically adjust control logic to optimise system outputs without requiring a full team of analysts.
Plan maintenance proactively, based on emerging wear patterns, not reactive triggers.
Reduce handoffs and guesswork with tools that provide aligned, cross-functional recommendations.
In high-performance environments like motorsport, it can mean simulating different pit strategies in real time or updating controller optimisation functions as conditions shift.
In oil & gas, it can mean continuously adjusting pump speeds or gas-lift settings based on predictive optimisation - keeping production stable while reducing energy waste.
The common thread?
These aren’t theoretical models. They’re practical systems, configured to fit the realities of your assets, constraints, and teams, and capable of making decisions at the speed your operations demand.
A Smarter Way Forward
You don’t need to build a data science team or start from scratch.
You just need tools designed for operational reality. Tools that make smart decisions faster to make, and easier to trust.
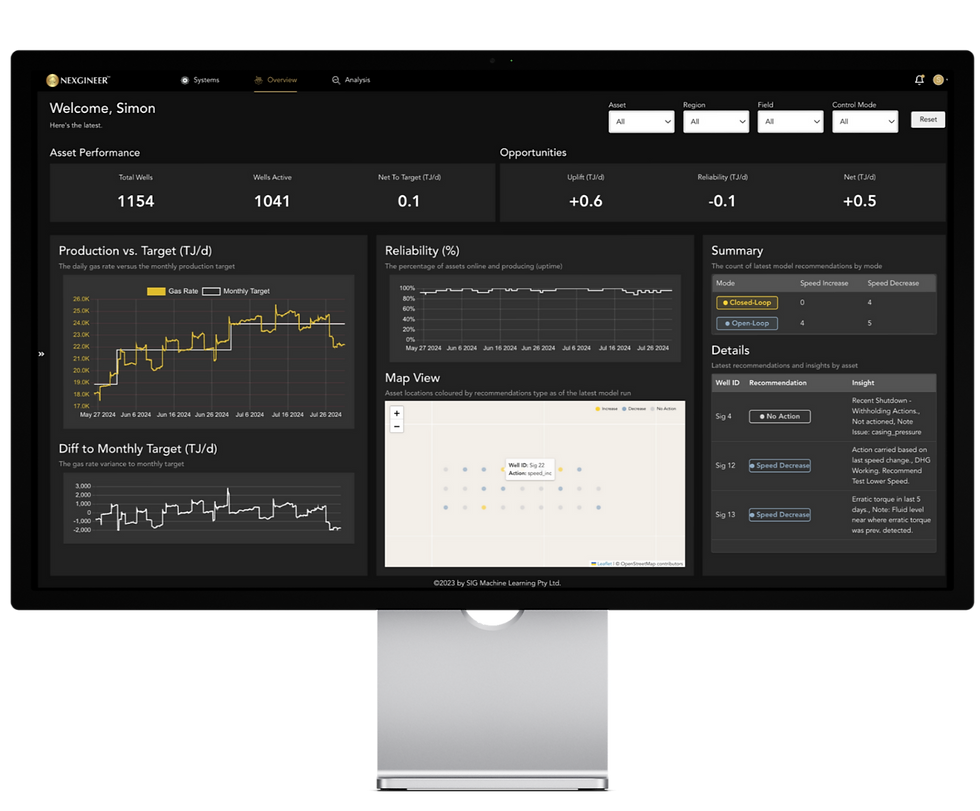
This is what we at SIG Machine Learning do best; making optimisation and control accessible rather than abstract. By partnering with teams in high performance industries we’re able to take the complexity out of applying AI, machine learning, optimisation modelling, and control system design, to deliver practical, easy to adopt solutions within engineering domains.
To do this we created Nexgineer™, a cloud-based software platform with built-in tools to simulate, automate, optimise, and scale in real-time and real-world scenarios. Nexgineer™ supports a range of targeted solutions for tasks like monitoring equipment, optimising processes, predicting maintenance, and improving control systems.
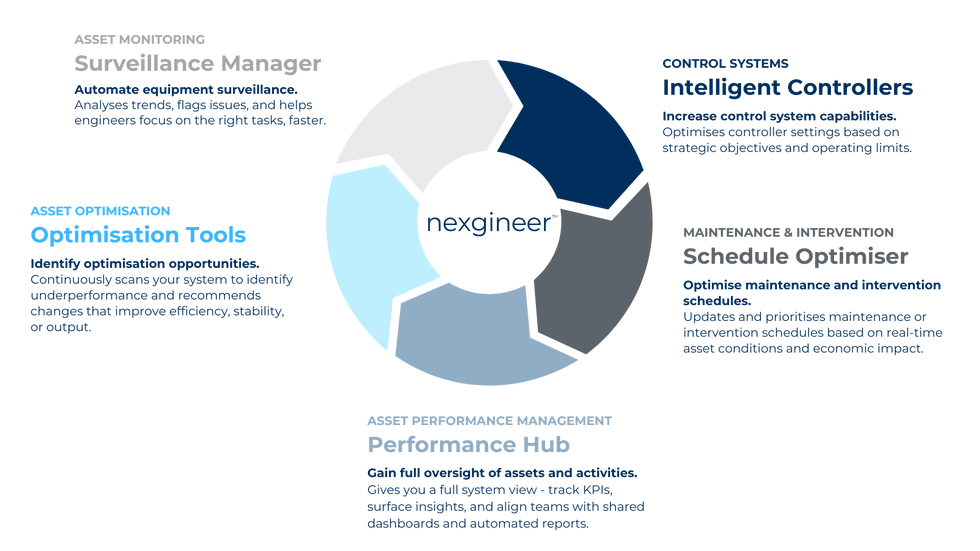
Nexgineer allows organisations to evolve beyond spreadsheets and dashboards and realise the value of their data - integrated within existing systems, and without disrupting their workflows.
It’s a proven way to move from reactive to proactive - from static insights to dynamic control.
Final Thought
If you’re starting to ask, “Could we be doing this better?” - the answer is probably yes.
And if you’re wondering what smarter optimisation might look like in your world, we’d love to explore it with you.